Raypa, founded in the 1970s by Ramón Espinar Aguilar, specializes in the manufacturing of equipment for sterilization in laboratories. Since the 1980s, the company has stood out in international markets. In 2008, the second generation of the Espinar family took over, adapting the company to new market needs.
With more than 40 years of experience, Raypa remains committed to quality and innovation, offering solutions for laboratories, hospitals, universities, and the food industry.
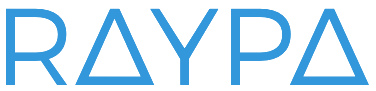
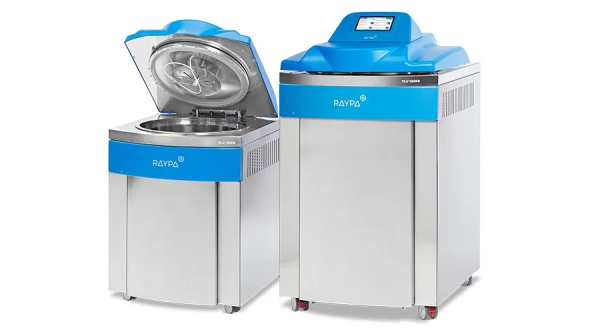
Raypa success story
We helped Raypa optimize the management of product photographs for customer shipments through a mobile application integrated with their SAP system, improving their processes and saving valuable time. This solution has increased operational efficiency, achieving a fast return on investment.

Challenge
The main problem was the manual management of product photographs for final customer shipments, a process that consumed a lot of time and was prone to errors. These photographs are essential for documenting the condition and quality of products before shipment, allowing customer claims to be resolved and ensuring that delivered products matched those shipped.
Additionally, they needed to integrate these images with their computerized management system, something their previous method did not allow efficiently. The previous process kept staff engaged in repetitive and low-value tasks, preventing them from focusing on more productive activities for the company. For this reason, Raypa sought a technological solution that could automate these tasks and optimize the use of their human resources.
The technological solution had to cover the following situations:
1. Automation of photograph management:
They required a way to capture and store product photographs in just a few steps to save time and reduce errors.
2. Integration with SAP:
They needed the photographs to be directly integrated into their management system to facilitate access and management within it.
3. Reduction of documentation errors:
It was important to decrease errors resulting from manual photograph management to improve accuracy and reliability in records.
4. Optimization of staff time:
They wanted to free their staff from repetitive and low-value tasks, allowing them to focus on more strategic and productive activities.

Solution
After analyzing Raypa’s needs and requirements, we at App2U recommended developing and implementing a custom app that would allow them to manage product photograph documentation quickly.
Development of a mobile application
We created an app that allows automatic capturing and storing of product photographs. This app is designed to be easily used by Raypa’s staff, enabling them to take pictures directly from their mobile devices. The automation of this process eliminated the need to manually capture and organize images, saving time and reducing errors.
Integration with SAP
We designed the application to integrate seamlessly with Raypa’s SAP system. This integration ensures that captured photographs are automatically stored in the management system, facilitating access and management directly from SAP. This guarantees that all visual documentation is centralized and easily available for use in various internal processes, such as product verification and claim resolution.

Result
Since Raypa and its team started using this application, they have seen a significant improvement in their operations. Thanks to the product photograph management app, the company has achieved the following results:
Reduction in management time:
Tasks that previously took hours are now completed in minutes. For example, capturing and manually managing photographs, which once took several hours, is now completed in minutes, freeing up valuable time for other activities.
Improvement in operational quality:
By automating tedious processes, Raypa’s team has saved time and improved accuracy in photograph management, reducing errors and enhancing documentation quality.
Application amortization:
The investment in the application was recovered in less than a year, achieving a return on investment in approximately 9 to 10 months. This quick return has allowed the company to enjoy significant financial benefits in a short period.
Adaptation to new needs:
The application is flexible and adapts to new business environment demands, allowing improvements and functionalities to be incorporated as additional needs are identified.